Vacuum Bonding & Other
Methods of Attachment
The following installation methods are used for the
application of ceramic tiles:
ADHESIVE
BONDING
- Two-part epoxy or Silicone Adhesives
- Vacuum Bonding
MECHANICAL
ATTACHMENT
- Weldable tiles
- Interlocking
VACUUM
BONDING TECHNOLOGY
Vacuum bonding is an advanced bonding
technology that combines specialty structural
adhesives, wear resistant materials and
controlled processing.
Applications which require high reliability,
high impact resistance and wear protection are
ideal candidates for vacuum bonding
solutions.
Vacuum bonding has been refined by Thermo
Vac into a state of the art technology which
gives bonding strengths which can never be
achieved with standard adhesives.
|
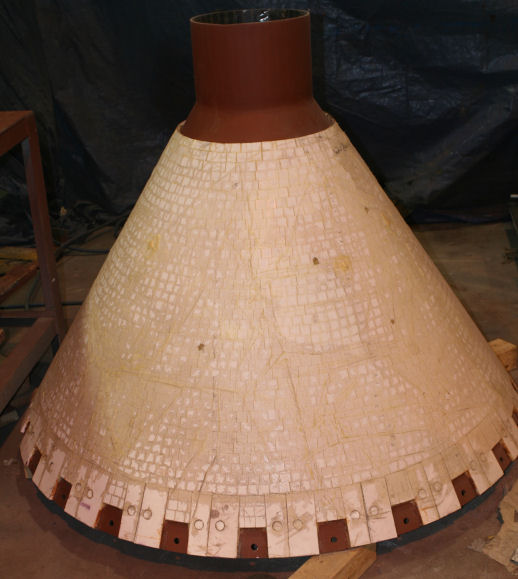 |
Valuable features of vacuum bonded materials are:
- Increased impact resistance of hard wear resistant
ceramics. (See our video!)
- Unparalleled performance in dynamic applications
- Extremely high sheer strengths
- Proven performance in light weight designs with ceramic
linings as thin as 6 mm thick
- Existing equipment and complex shapes are lined without
redesign
- Bonded linings can be machined to fit tolerances
- Extremely high reliability in critical moving
applications
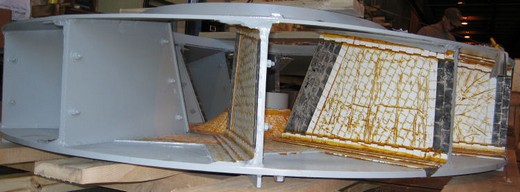
Vacuum bonding is an ideal solution in many tough
applications like:
- Fan blades
- Mixer housings and blades
- Valve gates
- Screw conveyors
- Pump volutes
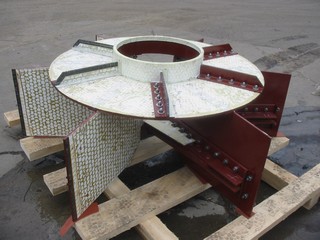
A summary of the Thermo Vac´s vacuum bonding technology
gives the following qualities:
- The only bond for dynamic applications
- Used in most power plant applications
- Excellent for dynamic applications with high
stress
- Increased resistance to impact and vibration
- Maximum temperature for dynamic applications 135
°C
- Maximum temperature for static applications 325 °C
- High shear and tensile strengths; 31 MPa shear and 41.5
MPa tensile
- Highest installed cost for ceramics
BRAZING
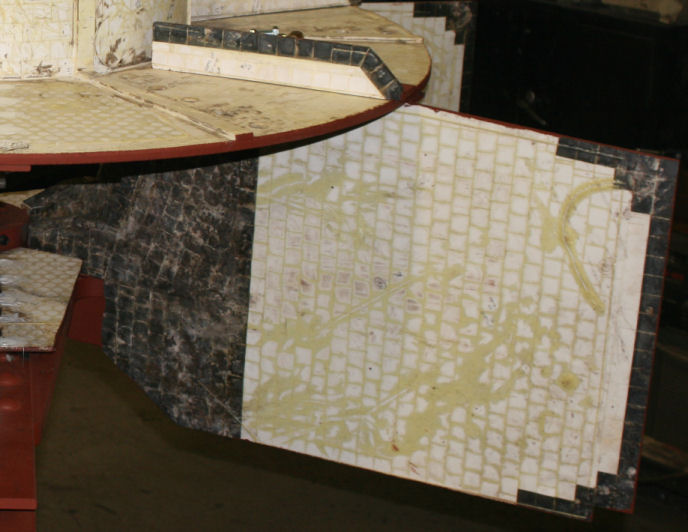 |
Brazing is used to attach tungsten carbide
to steel substrates.
Very high bond strengths are achieved; 280 -
500 MPa tensile and 175 MPa shear.
It has full bond strength at 1000 °C, and
excellent impact resistance.
|
COMPOSITE
TECHNOLOGY:
MECHANICAL
ATTACHMENT
Weldable clips or interlocking shapes can be
used with most wear materials.
The combination of standard adhesives and
mechanical attachment provides a cost effective
system for medium or low impact
applications.
|
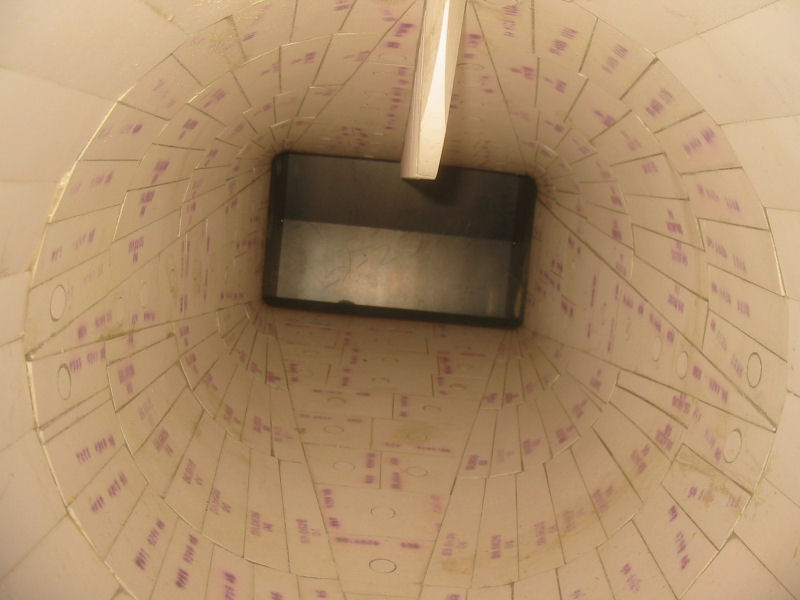 |
Summary of qualities:
- Mid-range installed cost for ceramics
- To be best used for static applications with medium
impact
- Secure attachment in higher temperatures
- To be used for applications with maximum temperatures
of 400°C
STANDARD
ADHESIVES
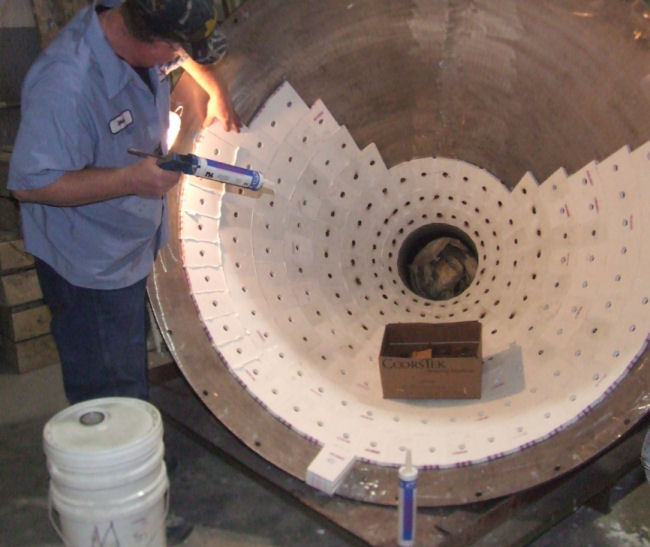 |
RTV Silicone and Two Part Epoxies are used
in low stress applications, usually together
with mechanically attached materials. Normal
maximum strengths are 7 MPa tensile and 5.5 MPa
shear.
RTV silicone is used in temperatures up to
260 °C and epoxy is used in temperatures up to
65 °C.
|
Summary of qualities:
- Lowest installed cost for ceramics
- To be used for static applications with low stress
- To be used for applications with minimal vibration or
impact
- To be used for applications with maximum temperatures
of 260 °C
- Low shear and tensile strengths; 5.5 MPa shear, 10 MPa
tensile
COMPOSITE TECHNOLOGY
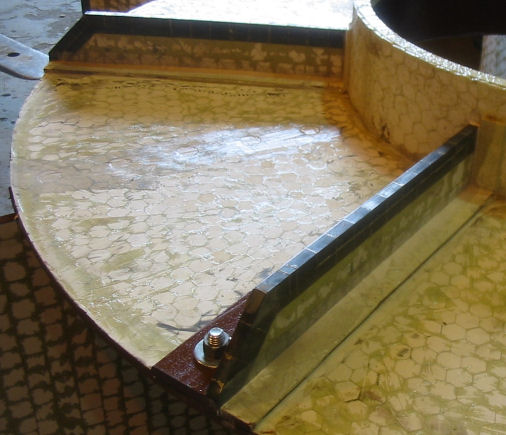 |
The composite technology uses a variety of
dissimilar materials that when bonded together
form a system which is superior to the
individual components.
This sytem puts the strongest wear materials in
the highest wear area and the more cost
effective materials in the less intensive
sreas, all on the same wear
surface.
|
|